「断トツライン」と「設計革命」
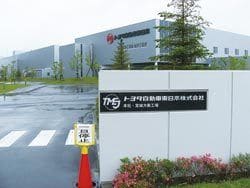
地道な活動であるものづくり面での改革で大きな取り組みは2つある。一つは「断トツライン」と呼ばれる生産性を極めて高めた現場づくりだ。2013年秋にトヨタの主力工場のひとつ高岡工場に導入された。すでに「断トツライン」の源流は、国内最新工場である子会社のトヨタ自動車東日本の宮城大衡工場(宮城県大衡村)にある。筆者も13年6月に取材に出かけた。あらゆる点に知恵を注ぎ込んだ工場だ。たとえば、車体をハンガーで吊るして流す方式をやめて、レールの上を流れる「自立式」に替えたことで、屋根を低く、かつ建屋の強度を落とすことができて投資コストを5割カットした。また需給や車種の変動に応じて生産ラインの長さを瞬時に短くできるラインにしたことで製造コストも激減、1ドル=80円台半ばでも国内生産で利益が出る体制を築いた。しかも、これまでは一つの工場で最低年産20万台ないと利益が出にくかった体質を、「断トツライン」の導入によって年産10万台でも利益が出るように改めた。
この生産量が落ちても利益が出る体質づくりは海外でも進んでいる。トヨタタイのバンポー工場で製造したピックアップトラックやSUV は世界100カ国に輸出されている。バンポー工場では、固定費という考え方はなく、すべての仕事にかかるコストを変動費として計算して事業環境の変化に強い工場運営にしている。この結果、稼働率が40%にまで低下しても利益が出る体質になった。非常に生産性が高い工場でもあり、何秒で1台を生産できるかを示すタクトタイムはバンポーでは56秒。日本のトヨタの工場よりもタクトタイムは早いときがある。工場内も徹底的に整理整頓が行き届き、トヨタ生産方式(TPS)の思想を徹底的に採り入れた工場運営をしている。
こうした取り組みなどによって、トヨタはリーマンショック後、総額1兆5000億円の原価低減効果を生み出し、同じく総額で1兆2000億円あった円高による為替差損を穴埋めした。リーマンショックの前に過剰設備・水膨れ体質になって、需要の変動が起きると一気に赤字に転落したことを反省しての取り組みとも言えるだろう。