「そよ風」のヒントとなったのが、(1)寺尾がモノづくりの勉強のために、町工場でお世話になっている頃、職人が扇風機の風を壁に当てて使っていたこと。(2)子供が二人三脚で競争する際、足の速い子は遅い子のほうに引っ張られて真っすぐに進むことができないという、事実だった。
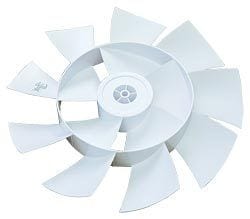
(1)については、自然界の風は、空気が大きな“面”で吹いているところに特徴がある。つまり、渦を巻く風から、面で移動する風に切り替えてやれば、そよ風を演出できる理屈だ。(2)は、「二人三脚」同様、速度の異なる2種類の風を隣り合わせで押し出せば、その速度や圧力の差によって気流が変化し、風が渦ではなく“面”になるかもしれない。
こうして閃いたアイデアが、2重構造の羽根となり、それを製品に落とし込む前の試作品づくりに大きな威力を発揮したのが、いわゆる“魔法の箱”であった。
「アイデアをデザインに起こし、その後、試作に持ち込む際、フルに活用したのが3Dプリンタでした。ここがダメ、そこがダメと、何度も試作品を使って、2重構造の羽根で風の流れを試しましたが、完成品に辿り着くまでに50個ぐらいは試作したと思います。試作を重ね、検討する、アナログ的な作業の繰り返しの中でしか、答えは生まれてこないのです」
寺尾がそう語るように、3Dプリンタなしに新型扇風機の製品化は難しかった。彼の目の前に置かれた試作品をじっと眺めたが、内側の羽根が5枚、外側の羽根が9枚で構成され、それらの羽根の1枚1枚の厚さに微妙な変化がつけられていることを知った。50個の試作品をつくったということは、50回の失敗を重ねた末に完成品に辿り着いたということで、3Dプリンタには、このように繰り返しできるメリットがある。従来の金型を使ったやり方では、3Dプリンタのように何度も試作品をつくることは至難の業で、膨大なコストと時間が必要だった。
従来、汎用品のモノづくりといえば、大企業などの大量生産モデルが一般的だったが、3Dプリンタを有効利用することで、ベンチャー企業はもちろんのこと、1人でもモノづくりの会社を創業できる可能性が高まってきた。