生産現場で「カイゼン」を重ね、品質向上とコスト低減を達成する「つくり込み」は、日本の「ものづくり」の得意技だが、韓国や中国をはじめ目覚ましい経済力の躍進をみせるアジア勢に肉薄されている。昨秋、タイで起きた大洪水で日本企業の現地工場が操業停止に追い込まれた際、国内工場で代替生産の指導に当たったのが来日したタイ人たちだったことは、まさに象徴的だ。いわゆる「六重苦」に代表されるコスト高の日本は、もはや「つくり込み」の力だけでは、戦いきれない。活路は、設計・開発から利用者へのアフターケアまで、追随を許さない製品やサービスを提供する「差別化」しかない。そのカギを握るのが、先端的な情報通信技術(ICT)を活用した新世代の「ものづくり」だ。
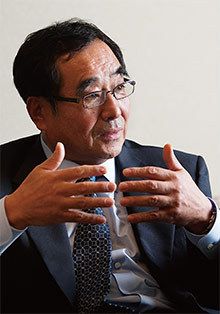
富士通相談役 黒川博昭氏
――「ものづくり」におけるアジア勢の追い上げが、急です。
【黒川】アジアが世界の「ものづくり」の最大拠点となった以上、それは当然です。市場自体も拡大し、日本企業も海外生産拠点の73%までをアジアに集中しています。同時に、日本勢はグローバルにみた生産拠点の最適配置を進めています。そのなかで、国内の工場をどう位置付けるかですが、いくつかの点から目指すべき道があります。
――どういう道でしょう?
【黒川】日本には、培ってきた「ものづくり」の基盤に加えて、世界有数の規模の市場があり、しかも成熟した高度な市場です。質の高い人材もいます。そうした強みを基盤として、企業連携や製品・サービスの高付加価値化を目指すのが、1つの道です。企業連携では、優れた技術力を持つ中小企業との連携や技術の集積も、重要です。
もう1つの道は、高付加価値化に必要な技術の創造や集積、流出防止による競争力の維持や強化のために、国内にマザー工場を持つことです。製品の量産は海外拠点で行っても、生産技術や人材の育成など「ものづくり」の核となる部分の高度化を国内のマザー工場に担わせれば、日本の「ものづくり」の優位性は維持できます。