国内約300社の部品メーカーから材料を調達している本田技研工業(ホンダ)が、輸送方法の見直しを検討している。その会計学上のポイントは、各社がホンダに対して個別に部品を輸送してきた点だ。
仮に1日に300社がホンダの工場に部品を納めにくるとすれば、工場では合計300回もの検品や納入の手続きを行うことになる。混乱を防ぐために納入の時間帯を6つに区切ったとしても、一つの時間帯で50社との対応が必要だ。また、1社が1台のトラックで運んできたら、50台分の駐車スペースも用意しなくてはならず、土地の有効利用の観点で疑問符がつく。
そこでホンダでは、自ら部品メーカーを回り、部品を集めて回ることを検討するという。ホンダが運送会社と大口の契約を結んでメーカーを回る方法などが考えられているようだが、そうなれば当然、コストが発生する。それでもホンダが自ら調達に回ったほうがいいのだろうか。
部品メーカーは納品にかかる物流費などのコストを部品の単価にのせている。しかし物流をホンダが担えば、部品メーカーは物流コストをカットでき、その分、ホンダの仕入れ価格は引き下げられる。たとえば、材料費300円、加工費400円、利益200円、物流費100円という部品があったとしよう。物流費が不要になれば、ホンダの調達価格は100円低くなる。
そうやって部品調達価格の値下がり分が、新規にホンダが負担する物流費を上回れば、トータルでのコストダウンにつながる。そんな方法があるのかと首をかしげるかもしれないが、解決策はある。たとえば、ミルク(牛乳)を効率的に運ぶ方法からネーミングされた「ミルクラン方式」という輸送方法だ。
ミルクを工場に運ぶ際、「酪農家Aからミルクを引き取って工場に持ち帰り、今度は酪農家Bへ引き取りにいく……」といった個別の輸送方式よりも、「A→B→C……」と回って、1台のトラックで一まとめに引き取ってきたほうが効率的という考え方である。コスト意識が極めて高いコンビニエンスストア業界のルート配送は“逆ミルクラン方式”といえるだろう。
実際には、先述したような部品メーカーのトラックを受け入れていた敷地を有効活用できるメリットや、検品・納入の手続きの簡素化にともなうコストの削減効果も試算する必要がある。ホンダでは現在よりも1~2割程度のコストダウンを見込み、今後1年程度かけて物流費の実態を調査したうえで決断するというが、このミルクラン方式を念頭に置いているはずだ。
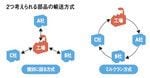
2つ考えらえれる部品の輸送方式
実はこうした物流費の削減は、ホンダをはじめとする自動車メーカーにとって非常に重要な経営戦略テーマだった。
2010年3月期のホンダの製造原価明細書を見ると、材料費(部品代)は1兆4444億円で、製品関係の製造原価全体の82.2%を占めている。ほかの自動車メーカーもおおむね80%程度で、自動車メーカーの原価における材料費の割合の高さがうかがえる。
特にホンダは部品の約70%を外部から調達しており、ほかのメーカーよりも外部調達比率が高いともいわれる。それだけ部品調達コストに含まれた間接的な物流費も大きく、輸送方式の抜本的な見直しによる経費削減効果が得やすいわけである。
このように会計情報を経営者の意思決定に役立てることを「管理会計」という。その管理会計において、部品調達の輸送を外注するか、内部化するかは、昔から議論の対象になってきた。
これまで見てきたように、物流費のマネジメントはコストダウン効果が高く、低成長時代のいまだからこそ取り組むべき課題ということができる。管理会計を積極的に活用していくことは、これから経営者に強く求められるだろう。