大阪府門真市にあるパナソニックのAVCネットワークス社を訪れて、設計・試作のいわゆる上流工程を担当する「生産技術センター」を見せてもらった。センターの一角に3台の3Dプリンタが置いてあり、うち1台がイヤーフックの試作品を製作中だった。3Dプリンタのインクジェットのヘッドから樹脂が吹きつけられ、肉眼では確認できないほどの薄い膜を積み上げていく。それは、あたかもケーキの上にホイップクリームを飾りつけていくように、ヘッドを動かしてひと筆書きをひたすら繰り返す作業である。
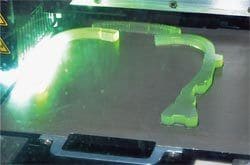
これまでのモノづくりは、溶かした樹脂などの原料を金型に流し込んで成形するのが一般的だった。金型の製作には、モノにもよるが1週間~10日程度の時間がかかり、いったん製品に不具合が見つかれば1からつくり直さなければならない。また、金型の製造コストは数十万円から100万円と高額であり、簡単につくり直しがきく代物ではない。それに対し、3Dプリンタは製作時間を大幅に短縮できるうえ、3Dデータさえあれば何度でもつくり直すことができる。
ウェアラブルカメラを世に出した第2商品設計グループ外装設計チームの村上智博チームリーダーは、これら一連のメリットをこう総括する。
「3Dデータがあれば、1日で積層できるこのスピード感はこれまでの工法にはないものです。試作ができた段階で、商品開発は言うに及ばずデザイナーや営業、マーケティングなどと、実際にモノを身につけて、手に取りながら課題を話し合うようなことも可能になりました。実際のカタチがわかるため、社内のコンセンサスも得やすい。3Dデータという技術者同士の共通言語が、試作の方法やスピードをガラリと変えてしまったことは間違いありません」
これはあくまでパナソニックのケースだが、ウェアラブルカメラを製作するに当たり、従来の金型を使ったものと、3Dプリンタを利用したものを比較した数字が出ている。それによると、
試作時間 90%減
試作費用 80%減
となり、驚くべき時間短縮とコスト削減につながったことが明らかになった。