ガスタービンの製造にも欠かせない
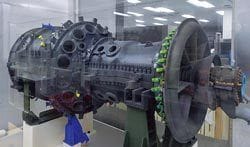
3Dプリンタで作製したガスタービン本体の模型。部品ごとに色分けすることで、部品の設置場所がよくわかる。
こうしたモノづくりの手法は、軽薄短小型のハイテク産業だけでなく、重厚長大型の“古い”産業にも及んでいる。
発電用ガスタービンの主力工場である三菱重工業の高砂製作所(兵庫県高砂市)。61年の製作開始以来、世界各国に600台近いガスタービンを出荷し、現在、米ゼネラル・エレクトリック(GE)、独シーメンスに次ぐ第3の位置につけている。
ガスタービンは全長15メートルもの巨大な装置だが、組み立ては100分の1ミリ単位の誤差も許されない精緻な加工技術やノウハウが要求される。三菱重工は07年以降、本格的に3Dプリンタを導入し、重工業におけるモノづくり革新を進めてきた。
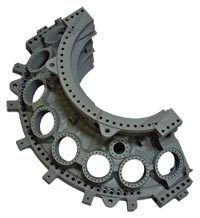
3Dプリンタで作製したガスタービンの羽根。
ガスタービンは、主に圧縮機、燃焼器、タービンの3つで構成される。圧縮機で圧縮された空気が燃焼器に送り込まれ、この高圧の空気に燃料の天然ガスを吹き込んで一気に燃やすことで、燃焼器からタービンへ高温高圧のガスが吐き出される。このガスをタービンの羽根が受け止めて回転させて、燃焼エネルギーが回転エネルギーに変わる。この回転エネルギーで発電機を回し、電気が生み出される仕組みだ。
その際、タービンの中で1000度を超える高温高圧のガスにさらされ続けるのが、燃焼器とタービンの羽根である。これらの中核部品の性能と信頼性をいかに高めるかが製品そのものの価値を決定することになり、羽根に100分の1ミリ単位の精度が求められるのも納得がいく。