派遣切りに始まり、製造ラインの一時停止、従業員の一時帰休など、製造現場の“受難”が続いている。
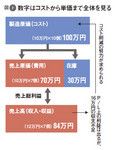
図7:数字はコストから単価まで全体を見る
製造の現場は、とかく日々の作業に追われ、経営上の数字と仕事との結びつきを他部署以上に感じにくい。景気がいいときは量産の喜びがあるが、不況時は冒頭のようなしわ寄せが来やすい。
しかも実態(数字)を共有する機会もないままに、在庫が膨らみ、突如こうした措置がとられたのでは納得することができない。「せっかく製造現場ががんばっても営業が弱いから売れない」「値引きばかりしているから儲けが出ない」などと、販売や経営サイドへの恨み節に発展しがちだ。
しかし、メーカーの根幹はつくることにあり、つくる人間自身が数字への理解を深めたらこれほど強いものはない。
なかでも大事なことは「全体との結びつき」を理解すること。製造工程で発生する「コスト」から、実際に製品が販売される「単価」まで、トータルで数字を理解してほしい。
![図8:製造原価の構成費比較で、ムダを見つける[製造原価比較]](https://president.ismcdn.jp/mwimgs/2/5/670wm/img_2522a41f0f1c78bec4dfdb3023729e1137373.jpg)
たとえば、原価10万円の製品を10個つくったとする(図7)。単価12万円で7個売れると売上高は84万円。売上原価となるのは、売れた分(70万円)だけなので、P/L上は利益が出る。ただし、支出を見ると、収入84万円に対し、支出は100万円となっており、16万円の不足になる。
つまり、製造コストは売上原価と在庫に分けられるゆえ、現場は在庫をも意識したコスト削減努力が求められる。そのため、B/Sの棚卸し資産(製品や原材料などの在庫)を注意して見ておきたい。倉庫に隠された“在庫リスク”の度合いをリアルに実感できるはずだ。決して容易なことではないが、こうした現場の努力こそが、会社の儲けにダイレクトに結びつくのだ。
また、コスト削減を考える際は、原材料費、労務費、経費といったコストがどれだけ発生しているのかを、まず把握しておく必要がある。
そこで覚えておきたいのが原価計算の考え方だ。つまり、P/Lに記されている「売上原価」の内訳を現場レベルで明らかにする。この作業で、削減するべきムダなコストも浮かび上がってくる。
実際には、自社のコストレポート(製品製造原価報告書)を手に入れ、材料費、労務費、経費の構成比を出してみるといい。製造現場で、どのコストが負担になっているのか把握できるはずだ。さらに、同業他社と比較することで、自社のコスト削減の余地や目安も探れる。
図8では、トヨタ、アサヒビール、サントリーの3社で製造原価を比較してみた。図のとおり、アサヒビールとサントリーは構成比が似ているが、金額ではアサヒビールのほうが経費や労務費のコストが高くなっている。また、トヨタの場合、労務費、経費に対して、原材料費の構成比が圧倒的に高く、変動費の比率が高いことがわかる(他社の製造原価は、決算書の単独P/Lの数値を参照)。